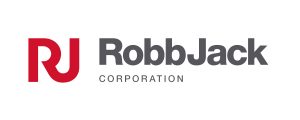
RobbJack's PCD Routers Headline Cutting Tool Engineering Magazine
Three main challenges exist when routing and trimming composite materials, according to Mike MacArthur, vice president of engineering for RobbJack Corp.: preventing uncut fibers, delamination of the composite layers and fiber pullout.
To machine composites, the Lincoln, Calif., toolmaker offers both diamond-coated carbide routers, in which diamond is grown on the cutting edges, and PCD routers. PCD blanks are either brazed onto cutter bodies or PCD slugs 3mm to 4mm thick (0.118″ to 0.157″) and then are cut to shape via electrical discharge grinding, MacArthur said. He noted about 60 percent of RobbJack’s tools for those applications are specials. “You can make them in all different kinds of configurations because of the advancement in solid diamond-tipped tools.”
Unless carbide routing tools are coated with actual diamond, he added, end users apply uncoated carbide tools—typically for finishing—because it’s difficult to justify the expense to deposit a coating that doesn’t last. “Even the amorphous diamond or DLC-type coatings wear off pretty quickly in carbon fiber and most composite materials.”
Numerous types of composites are available in which two or more materials—often with significantly different physical properties—are combined, including fiberglass, aramid, Kevlar and glass-reinforced plastic. One type tends to stand out. “We are seeing an increase in all types of composite materials, however, the vast majority are carbon fiber,” MacArthur said in reference to carbon fiber-reinforced polymers (CFRPs).
A vast number of industries have applications for composites, including energy, automotive and sporting goods. Once again, one sector dominates, according to MacArthur. “We are seeing huge increases across the board, but the biggest volume tends to be in aerospace.”
To help prevent delamination, as well as uncut fibers, MacArthur said RobbJack offers a router that provides a combination of upward and downward shearing flutes. This combination exerts a compression load on the workpiece material. “It is putting downforce on the top of the part and up force on the bottom.”
To determine the most-suitable tool to apply when machining composites, as well as other process variables, tool manufacturers often conduct tests in their in-house labs. The resulting information can save end users significant time and money.
“If a customer is doing a new part or new project, they could literally spend $30,000 on tooling just to figure out what the best solution is,” MacArthur said. “We have an in-house lab. A lot of our customers will send us a scrap part or some of their material. Then, for no charge, we will do some test cuts and very quickly determine what geometries work best.”
Routing a composite part in one pass, rather than taking roughing and finishing cuts to minimize the number of linear inches a router spends in the material, is one way to extend tool life and sharpness, according to RobbJack’s MacArthur. This approach also shortens cycle times.
“Once you start dulling the cutting edges or chipping the cutter or experiencing wear, you start adding a lot more friction and heat,” MacArthur said. “One key area of getting rid of the heat is to make sure that you’re maintaining a sharp tool as long as you can.”
As new composite materials are developed to enhance an ever-growing range of applications, parts manufacturers will continue to face different challenges when routing them. Cutting tool manufacturers, however, are not going to sit back and let them cut tomorrow’s composites with outdated routers.
“We constantly have to come up with different geometries, different coatings or combinations of geometries and coating to try and solve the issues our customers are having,” MacArthur said.
For the full Cutting Tool Engineering article, including pictures, click here.