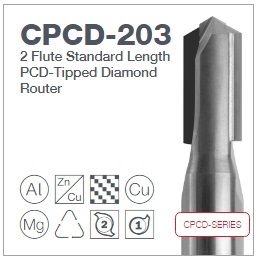
Trimming Carbon Fiber Aircraft Skins
Abstract
When trimming carbon fiber reinforced polymer (CFRP) aerospace skins, an aircraft manufacturer struggled with poor cycle times, poor tool life, and expensive scrap until switching to RobbJack’s CPCD diamond trimming tools
The Problem
Prized for its high rigidity and strength-to-weight ratio, CFRP is notoriously difficult to machine without delamination, uncut fibers and fiber pullout. One manufacturer was going through one carbide burr per part. They had to rough the part in two passes and then change the tool to abrasive diamond grinding tool to finish the part. Requiring 3 passes to finish the part.
RobbJack took on the challenge!
Our Solution:
CPCD-203 series PCD Trimming tool, Designed specifically for Composites.
The CPCD-203 Series PCD tool roughs and finishes the part in a single pass reducing the cycle time from 20 minutes down to 5 minutes 400% cycle time reduction.
- PCD lasts much longer than carbide from 982 carbide burrs per year down to 42 tools per year.
- Built in drill point allows the tool to plunge into the material without causing delamination on the exit
- New and revolutionary technology in the manufacture of PCD tools. This new technology improves tool quality, PCD adhesion to the tool body, and increases heat resistance during cutting. All of these improvements allow tool performance that was once impossible.
The Result:
- RobbJack’s CPCD-203 Series PCD router solved their trimming pains and was also able to achieve a cost savings of more than $216,000 per year.
- It completely stabilized and streamlined a previously difficult and wasteful process—secondary operations were no longer required
- Just one CPCD router was able to cut 23 parts —a process that previously had gone through 23 tools plus a finishing tools.
- The tooling cost per part went from $48 to $18 per part.
- They were able to keep up with demand and take on other jobs because we able to finish the job 4X faster.
The RobbJack CPCD-203 Series router consistently achieved clean, precise cuts. Plus, freed from the hassle and time of replacing worn tools, the manufacturer achieved increased capacity & throughput.
Total yearly savings $216,000