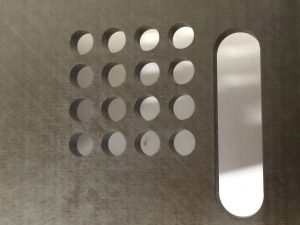
New Aerospace Materials Require New Cutting Tools
Our “W”-tipped drill cuts clean holes on CFRP-reinforced materials, compared to the rough edges left by conventional cutting tools.
Our W-Tipped Drill cuts clean holes on CFRP-reinforced materials
Our “W”-tipped drill cuts clean holes on CFRP-reinforced materials, compared to the rough edges left by conventional cutting tools.
Download a complete copy of the current US Applications Guide/Catalog
The introduction section of the RobbJack Application Guide/Catalog
Tools for working with aluminum. Click here for the guide.
Tools for working with titanium. Click here for the guide.
Tools for working with composites. Click here for the guide.
Tools for working in diemold applications. Click here for the guide.
Tools for working with miniature applications. Click here for the guide.
Tools for working in multiple applications. Click here for the guide.
Tools for working with wood and plastics. Click here for the guide.
“We have tools that reduce the amount of horsepower that’s consumed so you can remove more cubic inches per minute with the same amount of horsepower.” – Mike MacArthur
Download a copy of the current RobbJack pricelist with key product information
This end mill design enables it to vibrate at the same frequency as the workpiece, preventing vibration from turning into chatter.
At RobbJack, ingenuity is built into every tool, delivering performance the competition just can’t touch. Consider this recent automotive example.
When drilling carbon fiber–reinforced polymer (CFRP) wing spars, an aircraft manufacturer struggled with poor quality cuts and expensive scrap until switching to RobbJack’s new Solid PCD W-Point drill.
The new carbide material and new coating combination in RobbJack’s DM/MDM Die/Mold Carbide End Mill lasts 450% longer than comparable carbides and coatings designed for hard metal applications—and reduces wear by 909%.
A commercial airline manufacturer achieves 13,000 linear feet per tool trimming CFRP aircraft skins with CPCD-203
RobbJack end mills, saws, and router bits set the industry standard for close tolerances and consistent performance.
RobbJack SS and SR-Series micro end mills—when nothing less will cut it.
The proper way to choose a titanium tool. Also programming techniques and more. Click here.
Binding, slippage and high-torque cuts. What you need to know. Click here.
Carbide or steel shank? What’s the right order? How do I control heat? What’s the proper programming technique? All this and more here.
Machining aluminum? Here’s what you need to know to do the job right… the tools, the technique, the process
RobbJack Corporation manufactures rotary cutting tools from hard metal blanks containing none of the substances banned by EU RoHS directives. Click for a copy of our RoHS compliance letter.
RobbJack has sought and received representations from each of its suppliers that conflict minerals used do not originate in the Covered Countries, and have implemented measures for conflict-free sourcing. Click for a copy of our Conflict Mineral Template.
Solid Carbide Cutting Tools, PCD cutting Tools and Precision Ground Carbide Blanks, contain a chemical subject to section 313 of the Emergency Planning and Community Right-To-Know Act (EPCRA). Click for a copy of our notification letter.
The Hazard Communication Standard requires that RobbJack provide Safety Data Sheets (SDS) for each hazardous chemical to downstream users to communicate information on these hazards. Click to learn more and download our SDS.
Problems with chipping? T-process strengthens the cutting edge and helps eliminate chipping.
Need a tool with a full radius? Add a full radius to any end mill.
Modify any end mill with a Feather Blend™ neck to get the job done quickly and cleanly.
RobbJack’s Mirror Edge™ treatment dampens vibration to eliminate chatter.
Have cooling issues? Let RobbJack add coolant grooves to your favorite end mill.
DCC is a diamond coating that is produced in CVD chambers built by RobbJack’s sister company, Crystallume.
Our Black Widow DLC coating is tailored to have a combination of lubricity, abrasion, and corrosion resistance.
RobbJack’s TiN coating is optimized through a patented process to give you consistent coating properties.
The incorporation of carbon into the film increases its hardness and wear resistance, while lowering its coefficient of friction from the properties of TiN.
The development of PVD Aluminum Titanium Nitride based coatings is the most significant advancement in wear coatings since the introduction of Titanium Nitride.
All RobbJack Corporation products are manufactured wholly from solid carbide materials and do not contain any raw materials produced from, or substances derived of animal origin.
When the right cutting tool, toolholder, cutter paths and machining parameters are applied intelligently, a shop may have more capability to mill titanium effectively than it recognizes.
Composite tools present their own special challenges, such as proper fixturing and vibration. And of course, it always helps to get the best tool for maximum life
Carbon Fiber and other composite materials are very difficult to cut with out delamination, uncut fibers, or poor tool life. This webinar teaches techniques to solve those problems. This webinar covers diamond coated carbide, PCD, and carbide routers and drills.
Quick, easy speed and feed calculations for any material, grade or machining application in both metric and standard.
Choosing the right tool will pay huge dividends in the quality, repeatability and the overall success of a job. This article discusses the different types of materials, which tools to choose, and how to use them.
Many people feel that hard metal machining is a black art, but with a few basic principles it is not only profitable but also a straightforward machining process.
Use this form to easily calculate your actual savings when applying our tools to your specific applications. Download this Excel version that does all the calculations for you! (Requires MS Excel)
With the right tools and a little know-how, you can remove a lot of metal in a shorter time than you thought possible.
Trochoidal toolpaths are available on most CAD/CAM systems, yet are rarely used or even known. By using trochoidal toolpaths and hybrid trochoidal toolpaths you can successfully machine exotic materials.
Many of the proven technologies used for mold and die machining can also be used in difficult to machine aerospace materials.